Technologie přehled
Technologie - stručný přehled po tématech
J. Šimůnek
Měření je jednou ze základních operací při ručním zpracování kovů. Při měření porovnáváme rozměr určitého předmětu s velikostí tzv. měřící jednotky.
Měření skutečných hodnot - skutečnou hodnotu měříme
universálními měřidly, na nichž je možno přímo odečítat naměřené hodnoty vpříslušných jednotkách. (ocelové měřítko, posuvné měřítko, mikrometr atd.
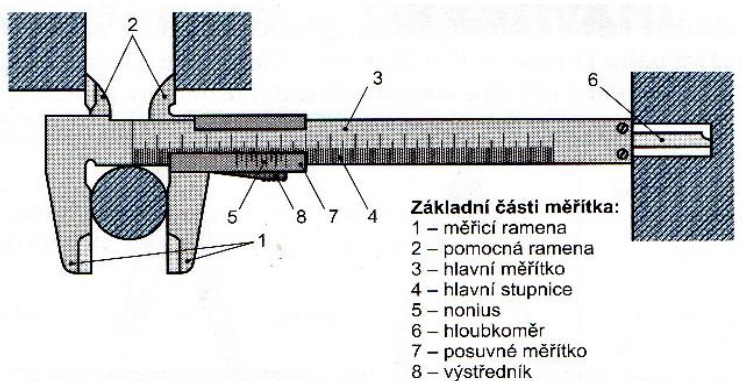
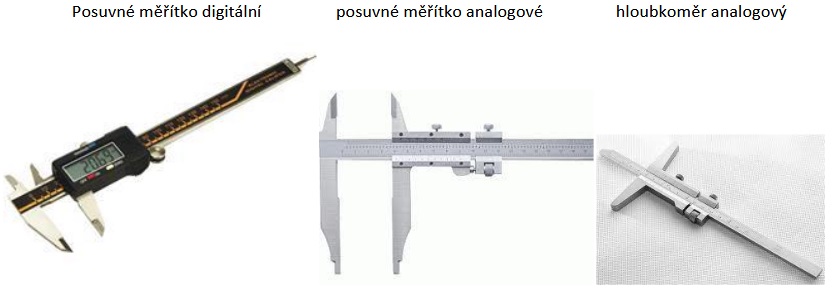
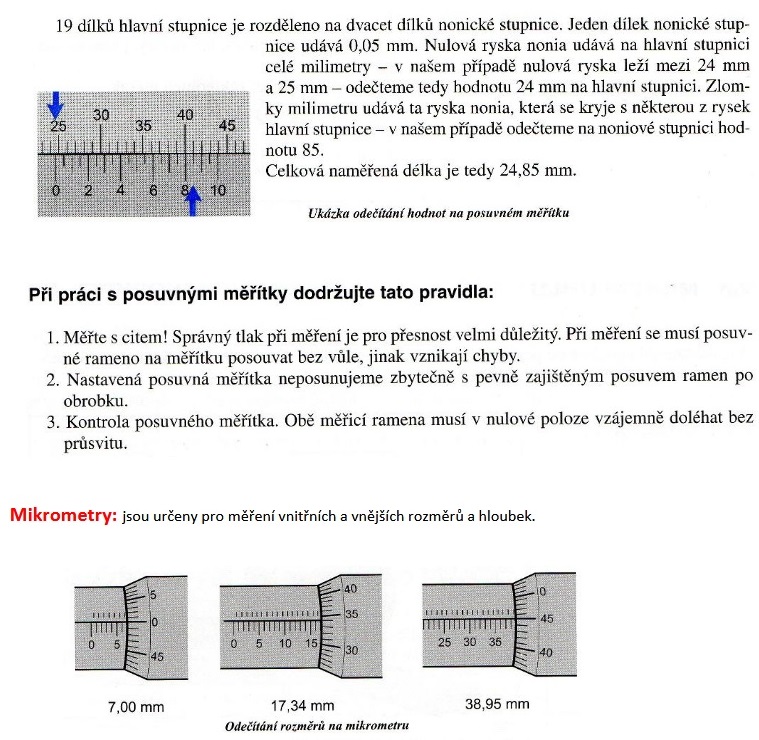
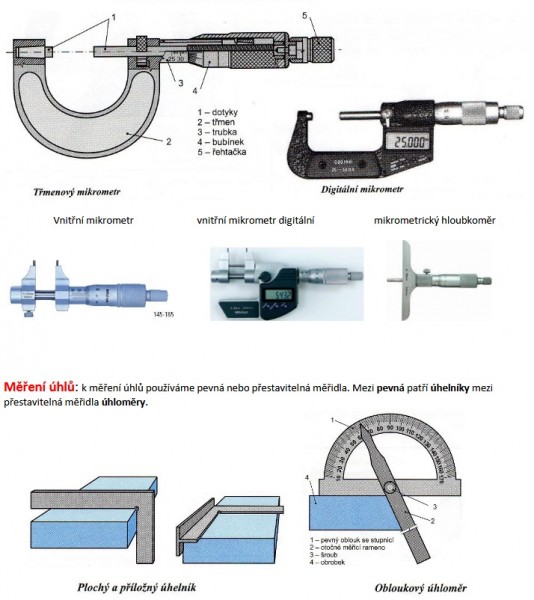
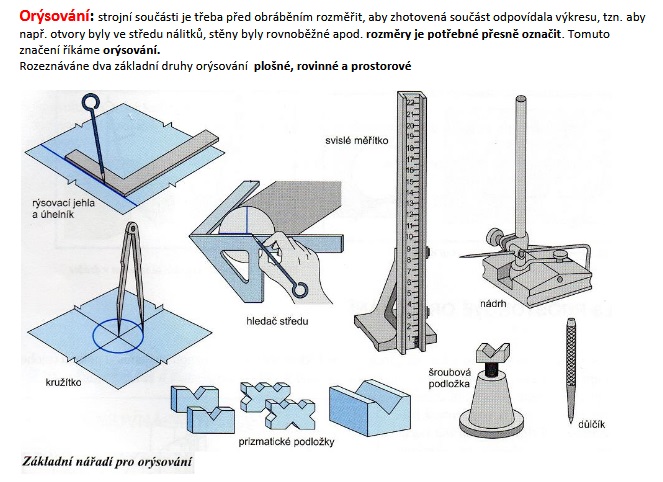

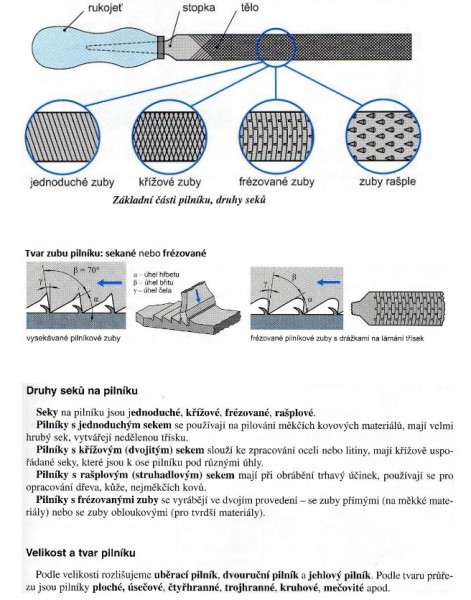
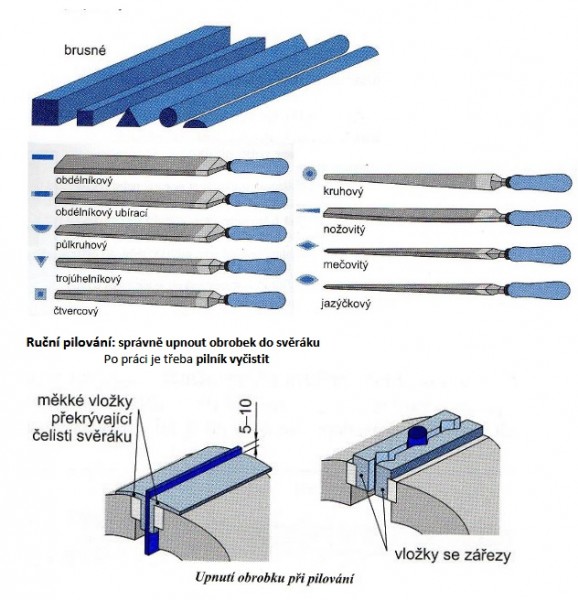
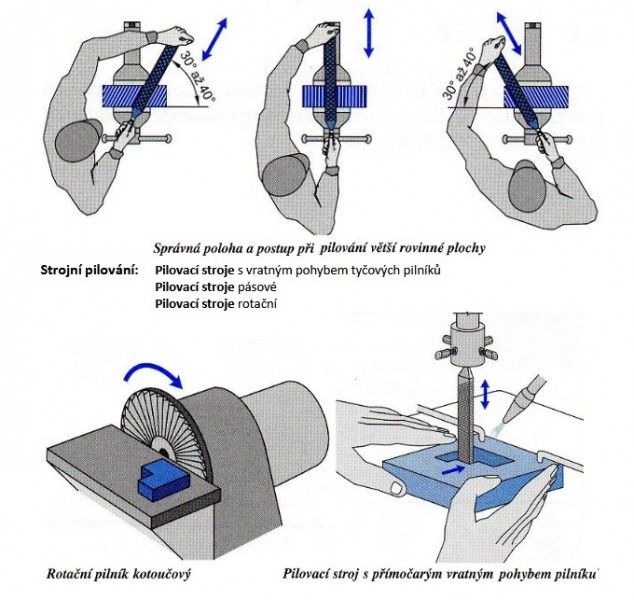
Rukojeť pilníku nesmí být prasklá, ani jinak poškozená.
Kontrolní otázky:
podle čeho volíme správné druhy pilníků?
Popište správné upínání obrobků při pilování?
Jaké druhy seků mají pilníky?
Řezání ruční rámovou pilkou
• Pilový list se upíná do rámu pilky pomocí čepů nebo nýtů
• Napínáme křídovou maticí
• Špičky zubů směřují od rukojeti
• Zuby listu jsou kalené a vyhnuté
• Pro zmenšení tření můžeme mazat strany listu řezným olejem
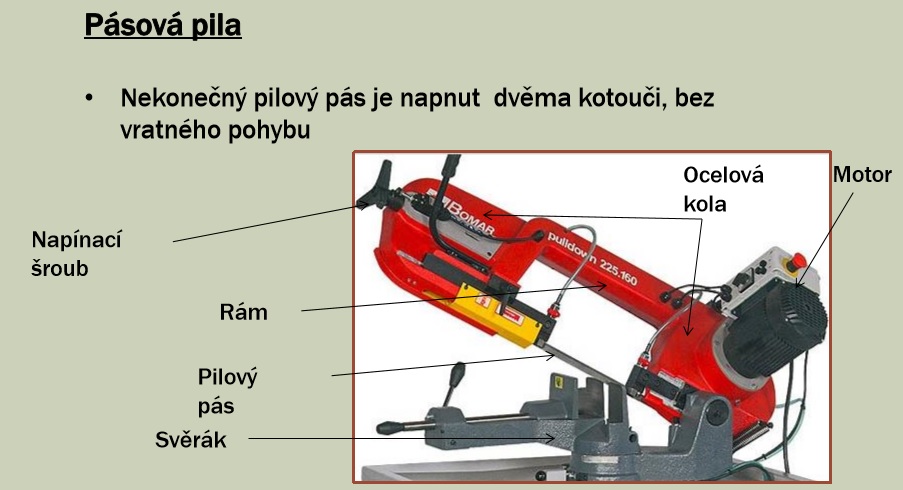
Kotoučová pila
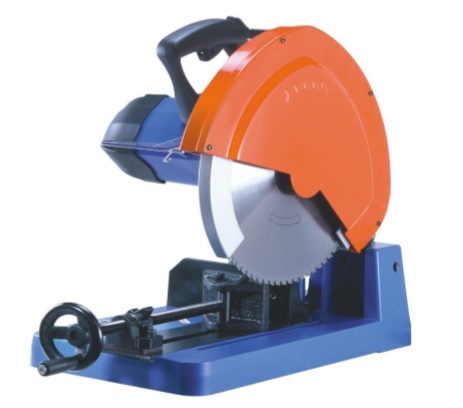
Strojní rozbrušovací pila
nástroj rozbrušovací nebo diamantový kotouč
Ruční úhlová bruska
po výměně brusného kotouče za řezací lze použít brusku k řezání
Kontrolní otázky:
• Popiš hlavní části ruční pilky
• Popiš hlavní části strojní pásové pily
• Jaký je rozdíl mezi pásovou a kotoučovou pilou
• Jak lze použít úhlovou brusku
Nástroje na pájení:
Nástroje, kterými se taví pájka, se nazývají: Nástroje na pájení: pájedla- jsou to měděné hroty vhodného tvaru a velikosti, uchycené v držáku, ohřívané v peci nebo jiném topném zařízení. Velikost a tvar měděného hrotu závisí na druhu práce pro níž je tvar určen. Čím je měděný hrot větší, tím více tepla akumuluje, takže se nemusí příliš zahřívat. Pro hrubší práce se používají větší hroty, pro jemné práce hroty menších rozměrů. -páječky- mají vlastní zdroj tepla trvale zabudovaný a) elektrické b)benzínové c) plynové
Měkké pájky Jsou to slitiny cínu, olova a antimonu. Mají poměrně nízkou teplotu tavení ( pod 450°C ). Používají se na tuhé spojení kovových součástí, k utěsňování otvorů a spár, k vyplňování dutin a k pokovování. Jsou vhodné na spojování plechů: ocelových zinkových olověných měděných pozinkovaných poolověných
Měkké pájky se dodávají: - v tyčích litých a tvářených - jako drát - v pásech a fóliích - jako vlákna - v pájecích prášcích - v pájecích pastách
Tavidla Jsou nekovové látky, které odstraňují oxidy z pájeného povrchu a zamezují jejich nové tvorbě. Dále se užívají k chemickému očištění spojovaných kovů a hrotů páječek od nečistot. V klempířské praxi se používají tavidla: • chlorid amonný ( salmiak ) • zředěná kyselina chlorovodíková ( solná) • chlorid zinečnatý (pájecí voda) • kalafuna • pájecí pasta
Způsoby měkkého pájení • pájení pájedlem nebo páječkou • pájení plamenem • pájením ponořením • pájení poléváním • pájení v peci • odporové pájení • pájení ,,stojatou´´ vlnou • indukční pájení • blokové pájení
Postup při pájení na měkko Místo spoje očistíme mechanicky i chemicky. Pro kvalitu spoje je důležité, aby tavidlo vniklo na celou plochu spojovaných částí. Hrot páječky očistíme a pocínujeme, spojované předměty ohřejeme asi na 100°C a potom naneseme pájku na předmět, tak aby protekla celou spárou a zaplnila ji. Pájku nanášíme hrotem páječky. Po spájení se spoj a jeho okolí omyje teplou vodou, aby se odstranily zbytky tavidla.
Tvrdé pájení s tavidlem ,v ochranném plynu nebo ve vakuu, se podobá pájení na měkko. Pracovní teplota je nad 500°C. Pájí se tvrdou pájkou, roztavenou plamenem. Pájet je možno součásti ze stejných nebo různých materiálů, zahřátých na pájecí teplotu. Základní materiál se při pájení na tvrdo nesmí tavit, tvrdá pájka tedy musí mít nižší teplotu tavení než základní materiál. Součást se spojí, když pájka přejde do základního materiálu. Pevnost spoje je dána pevností mezivrstvy, v níž je pájka smíšena se základním materiálem.
Pro pájení na tvrdo potřebujeme: • Pájku • Tavidlo • Zdroj tepla
Tvrdé pájky Musí mít dobré mechanické vlastnosti, musí dobře smáčet pájené plochy a musí k nim vždy dobře přilnout. Mají být tak tekuté, aby bylo možné pájet ve všech polohách.
Tvrdé pájky Musí mít dobré mechanické vlastnosti, musí dobře smáčet pájené plochy a musí k nim vždy dobře přilnout. Mají být tak tekuté, aby bylo možné pájet ve všech polohách. V praxi se nejčastěji používají mosazné a stříbrné tvrdé pájky, které se dodávají v drátech, zrnech, litých tyčích, pásech a pruzích. Mosazné pájky- jsou ze slitiny mědi a zinku, používají se u materiálů z oceli a niklu a také u jejich slitin. Pracovní teploty se pohybují mezi 710°C a 1100°C.
Stříbrné pájky- jsou ze slitiny mědi, zinku a stříbra. Pájky s obsahem stříbra menším než 20% se používají u materiálů citlivých na teplo např. u mědi. Pracovní teplota se pohybuje mezi 710°C – 880°C. Pájky s obsahem s minimálním obsahem stříbra 20% obsahují Ag, Cd, Cu, Zn, Sn, Mn, Ni a jsou používány k připájení slinutých karbidů. Pracovní teploty jsou mezi 610°C až 960°C.
Tavidla Jsou látky, které používáme na očištění pájených kovů od nečistot a oxidů, protože roztavená pájka přilne jen na čistý povrch. Tavidla rozpouští nečistoty na pájených plochách, snižují bod tavení vzniklých oxidů, Chrání plochy před okysličením a před zplodinami hoření. Při pájení natvrdo se jako tavidla nejčastěji používá borax – tetraboritan sodný, který se taví při teplotě 783°C.
Pro vyšší pracovní teploty přidáváme do tavidla kyselinu boritou, pro nižší pracovní teploty snižujeme tavitelnost přísadou chloridu zinečnatého. Kromě boraxu se jako tavidla používají i soli fosforu a soli halových prvků. Tavidlo se dodává ve formě prášku nebo pasty.
Zdroj tepla • Plameny různých plynových hořáků - kyslíko-acetilenový - vzducho-acetilenový - vzducho-svítiplynový • Plamen benzínové lampy • Plamen kovářské výhně
Způsoby tvrdého pájení • pájení plamenem • pájením ponořením • pájení v peci • pájení v ohni • pájení v solné lázni • pájení odporovým ohřevem • pájení indukčním ohřevem • Pájení kapilární
Postup připájení na tvrdo Zoxidované vrstvy se odstraní škrabáky a řádně očistíme. Plamenem nahřejeme připravené plochy na potřebnou teplotu. Po nahřátí nanášíme pájku podobně jako při svařování plamenem. Pájecí tyčinka a pájené plochy musí být vždy dobře pokryty tavidlem. Příliš nízká nebo příliš vysoká teplota pájených ploch může způsobit, že roztavená pájka pájené plochy dokonala nesmáčí .Pájení na tvrdo se používá ke spojování takových kovů, které nelze
dobře pájet na měkko např. bronz, mosaz, litina a některé druhy oceli, dále k pájení různých slitin např. ocel s mědí, ocel s mosazí, měď s mosazí atd. a takových kovů, které by se svařováním poškodily.
Svařování plamenem 2.2
Autogen - plamenové svařování, kyslíko-acetylénové svařování
Autogen nebo-li svařování plamenem, patří mezi tzv. tavné metody svařování. Metoda využívá teplo dodávané spalováním směsi hořlavého plynu a kyslíku nebo vzduchu pro natavení svarových ploch a roztavení přídavného materiálu.
Pro svařování se nejčastěji používá směs acetylénu a kyslíku, protože tato směs ve správném poměru umožňuje dosáhnout teploty plamene až okolo 3200°C. Jako hořlavý plyn lze využít i vodík nebo propan, ale teplota plamene je nižší ( maximálně 2500°C). To stačí ke svařování –pájení kovů s nižší teplotou tavení jako je hliník, měď, hořčík nebo olovo, tepelné zpracování svařenců a pro čištění povrchů plamenem.
Použití
Nejvhodnější pro svařování ocelí je kyslíko-acetylenový plamen, jiné směsi hořlavých plynů a kyslíku nebo vzduchu se používají pro kovy s nižší teplotou tavení. S drobnými rozdíly ve vybavení a použití směsi plynů se podobná technika využívá i při plamenovém řezání kovů kyslíkem.
Jako přídavný materiál se používají svařovací dráty stejného nebo podobného chemického složení jako svařovaný základní materiál. Na kvalitě přídavného materiálu závisí i kvalita hotového svaru. Ocelové svařovací dráty bývají poměděné kvůli ochraně proti korozi. Průměry svařovacích drátů odpovídají tloušťce svařovaného základního materiálu.
Postupy při svařování plamenem
- Svařování vpřed - svařovací drát je veden před hořákem ve směru svařování, vhodné pro tenké plechy do tloušťky 4 mm.
- Svařování vzad - svařovací drát postupuje za hořákem, plamen je směrován na tavnou lázeň i na chladnoucí svar. Dochází tím k ochraně tavné lázně i tuhnoucího svaru, způsob je předepsaný pro namáhané svary nejrůznějších konstrukcí.
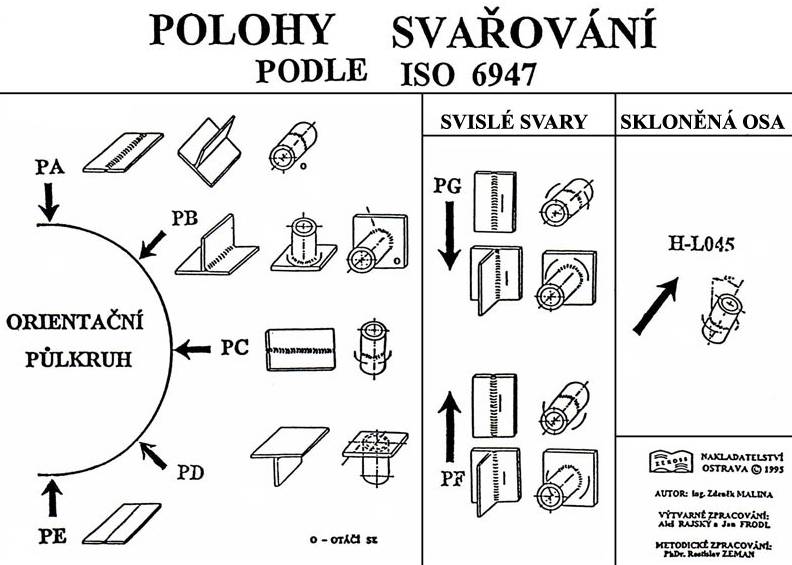
- bazické, rutilové, speciální elektrody,
- dráty pro MIG/MAG svařování,
- dráty pro TIG svařování
- dráty pro svařování plamenem,
- pájky pro měkké a tvrdé pájení,
- tavidla.
Obloukové svařování obalenou elektrodou, svařování MMA, svařovací technika, svařovací invertor
Jedna z nejstarších technologií svařování. Obloukové svařování obalenou elektrodou je manuální proces, kde zdrojem tepla je elektrický oblouk. V okamžiku zážehu oblouku mezi elektrodou a svařovaným materiálem vzniká vysoká teplota, která roztavuje jak materiál elektrody, tak i základní materiál.
Složení elektrody
Obalená elektroda je složena z plného materiálu tzv. jádra a obalového materiálu. Jádro elektrody pak tvoří nezbytnou složku přídavného materiálu. Další funkční složkou je obalový materiál elektrody, který zabezpečuje ochranu svarové lázně a vytváří tak ochranou atmosféru a strusku. Při procesu chladnutí je pak svar chráněn povrchovou struskou. Po procesu chladnutí je doporučeno strusku odstranit.
Výraznou inovací principu této metody je obloukové svařování plněnou elektrodou bez ochranného plynu (metoda 114 podle ISO 4063 ). Místo elektrody obalenou tavidlem se používá trubičkový drát naplněný tavidlem navinutý na cívce. Tavidlo i v tomto případě zajišťuje vznik ochranné atmosféry.
Použití
Technologie se využívá zejména pro svařování ocelových konstrukcí, tlakových nádob nebo v lodním průmyslu. Při práci s vyšší sériovostí je třeba použít svařovací procesy, které jsou snadněji mechanizovatelné (např. MIG/MAG). Metoda je použitelná na svařování běžných uhlíkových ocelí, nerezových ocelí, litiny, hliníku (hliníkových slitin), niklu (niklových slitin) a mědi. V současné době je její nasazení omezováno z důvodu nízké výkonnosti a nutnosti velmi dobré manuální zručnosti svářeče.
Výhody metody MMA:
- zařízení pro MMA je relativně jednoduché a přenosné
- metoda nevyžaduje externí zařízení plynového hospodářství
- proces je relativně nenáchylný na povětrnostní podmínky jako např. odfouknutí plynu
- proces může být použitý i v podmínkách s nižším nárokem na přístup
- různorodá použitelnost v oblasti druhů materiálů (uhlíková ocel, slitiny, nerez, litina, hliník apod.)
- možnost svařování v polohách
Nevýhody metody MMA:
- nutnost odstranění strusky z povrchu materiálu
- nízká produktivita z hlediska častých výměn elektrod
- metoda není vhodná na povrchově upravené materiály jako Ti, Zn
- metodu nelze aplikovat na reaktivní prvky
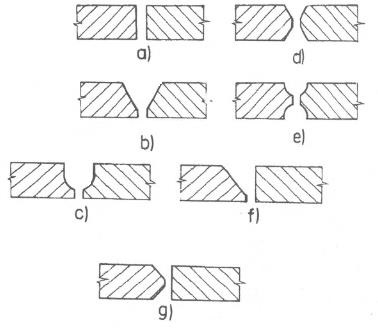
Obrázek 1: Svary tupé: a) svar I, b) svar V, c) svar U, d) svar X, e) svar UU, f) svar ½ V, g) svar ½ X
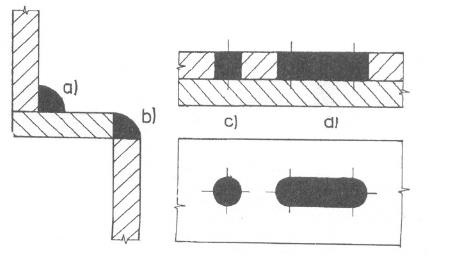
Provedení svarových spojů:
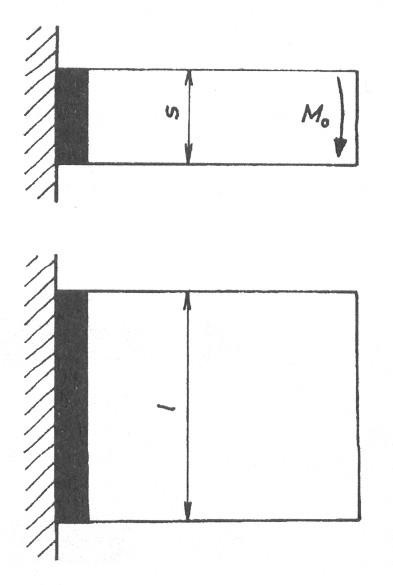
Obrázek 3: Spojení ploché části tupým svarem I
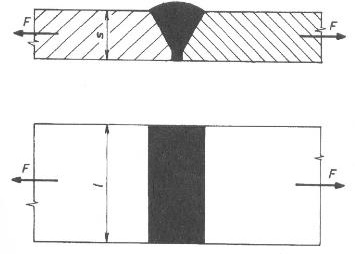
Obrázek 4: Spojení dvou plochých částí tupým svarem V
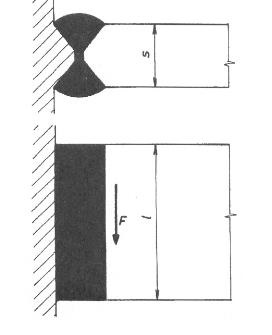
Obrázek 5: Spojení ploché části pomocí svaru X
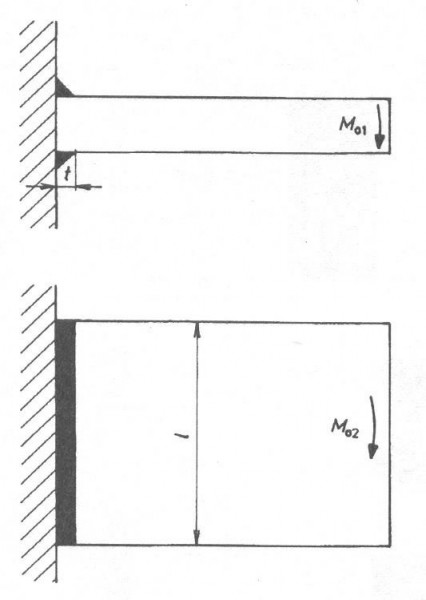
Obrázek 6: Uchycení ploché součást na svislou stěnu pomocí koutového svaru
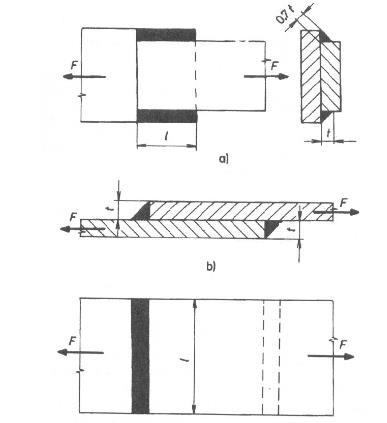
Obrázek 7: Dva případy spojení plochých částí pomocí koutových svarů: a) svar na bocích užších částí, b) na čelech obou částí
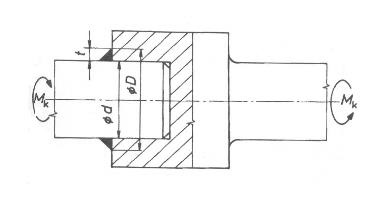
Obrázek 8: Spojení dvou rotačních částí koutovým svarem
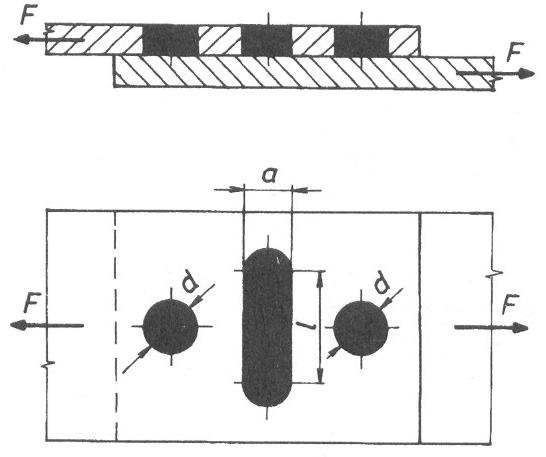
Obrázek 9: Spojení dvou plochých částí pomocí děrového a žlábkového svaru
Výhody metody MIG/MAG - svařování ve všech svařovacích polohách, vysoká svařovací rychlost, nižší nároky na čištění strusky, eliminace zplodin, oblouk i svarová lázeň je jasně viditelná, menší deformace po svařování.
Obloukové svařování v ochranné atmosféře plynů
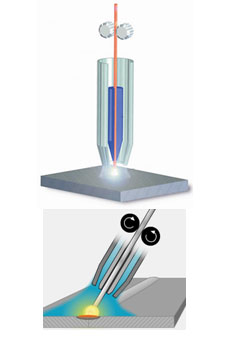
Při svařování v ochranné atmosféře plynu (GMAW - Gas Metal Arc Welding, MIG - Metal Inert Gas, MAG - Metal Active Gas) vzniká oblouk mezi nepřetržitým svařovacím drátem a svařencem.
Oblouk a svarová lázeň jsou chráněny proudem inertního nebo aktivního plynu.
Tato metoda se hodí pro většinu materiálů a přídavné materiály jsou k dispozici pro široký sortiment kovů.
Svařování MIG/MAG je podstatně produktivnější než MMA - ručně obalenou elektrodou, kde se produktivita ztrácí pokaždé, když svářeč zastaví, aby vyměnil spotřebovanou elektrodu. Při MMA vznikají také materiální ztráty při vyhazování nedopalků. Z každého kilogramu prodané obalené elektrody se asi jen 65 % stane součástí svaru (zbytek se vyhodí). U svařování MIG/MAG se používáním svařovacího plného či trubičkového drátu účinnost zvýšila na 80-95 %.
Svařování MIG/MAG je univerzální metoda, kterou je možno ukládat svarový kov ve větším množství a ve všech svařovacích polohách. Používá se pro svařování velmi lehkých až středně těžkých ocelových konstrukcí a nerezových ocelí (MAG), pro svařování slitin hliníku či mědi (MIG) a zvláště tam, kde se vyžaduje vysoký podíl ruční práce svářeče nahradit automatizací.
Obloukové svařování plněnou (trubičkovou) elektrodou
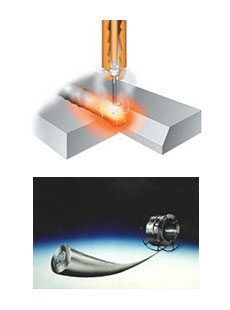
Pokud jde o práci a zařízení, je svařování trubičkovým drátem (FCAW - Flux Cored Arc Welding, dle normy správněji svařování plněnou elektrodou) velmi podobné svařování MIG/MAG. Nesvařuje se však plným drátem nebo elektrodou, ale je to kovový plášť vyplněný tavidlem nebo látkou, která chrání svarovou lázeň podobně jako ochranný plyn. Náplň některých druhů trubiček však může být koncipována i tak, že při svařování vzniká vlastní ochranná atmosféra a samostatný přívod ochranného plynu není potřebný.
Plněné dráty se svinují z plechů s podélným švem jako tvarově uzavřené nebo bezešvé, podélně vysokofrekvenčně svařené. Pláště se vyrábějí většinou z nízkouhlíkové oceli.
Současné trubičkové dráty se dodávají se struskou nebo bez strusky. Struskotvorné plněné dráty pracují podobně jako obalené elektrody, bezstruskové mají jako náplň kovový prášek.
Základní přednosti plněného drátu proti plným drátům jsou :
- hlubší závar
- nízká náchylnost na tvorbu pórů
- malý rozstřik
- vyšší výkon odtavení ( až 40% navýšení )
Nejpoužívanější typy průřezů plněných drátů jsou :
-
bezešvé plněné dráty
- tvarově uzavřené plněné dráty
Trubičkové dráty lze používat na standardním zařízení, ale za daného proudu bude rychlost podávání drátu mnohem vyšší ve srovnání se stejným průměrem plného drátu.
Jako u svařování MIG/MAG závisí i tato metoda na ochranném plynu, který chrání svarovou oblast roztaveného kovu. Plyn se dodává buď samostatně (trubičkový drát je určen pro svařování v ochranné atmosféře) nebo vzniká rozkladem přísad z náplně (trubičkový drát s vlastní atmosférou). Kromě ochranného plynu produkuje trubičkový drát strusku, která slouží jako další ochrana při chladnutí svarového kovu a poté se z jeho povrchu odstraní.
Relativně malé rozšíření plněných elektrod ve svařovacích provozech je způsobeno jejich vyšší pořizovací cenou.
Svařování TIG WIG 2.10
Svařování TIG, svářečky TIG (WIG), svařovací zdroje TIG, sváření TIG, TIG svářečka
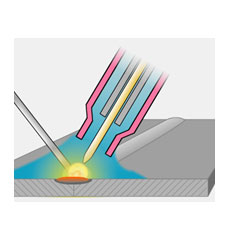
GTAW ( Gas Tunsten Arc Welding) - americká zkratka, TIG ( Tungsten Inert Gas)-anglická zkratka, WIG( Wolfram Inert Gas) – německá zkratka metody, při které oblouk hoří mezi základním materiálem a netavnou wolframovou elektrodou v ochraně inertního plynu. Přídavný materiál je do oblouku podáván samostatně ručně až automaticky nebo proces svařování probíhá pouze roztavením a slitím základních materiálů.
Nevzniká žádná struska, je sníženo na minimum riziko vměstků ve svarovém kovu a hotové svary nevyžadují žádné čištění. Metodu TIG ( WIG ) lze použít téměř pro všechny kovy a hodí se jak pro ruční, mechanizované i automatizované svařování.
Nejvíce se užívá na svařování hliníku a nerezavějících ocelí, u vytváření vysoce kvalitních spojů.
Svařovací zdroje využívají :
- Stejnosměrný svařovací proud – DC; zapojení na přímou nebo nepřímou polaritu; použití pro ocel, měď, titan a jejich slitiny
- Střídavý svařovací proud – AC; svařování hliníku, hořčíku a jejich slitin
Nejznámějšími svařovacími zdroji jsou invertorové svářečky, které mají nízkou hmotnost, malé rozměry a vysoké výkony. Mohou být dovybaveny funkcí pro řízení dodávky ochranného plynu – předfuk a dofuk plynu, funkcí pro dvoutaktní nebo čtyřtaktní proces svařování, funkcí dokonalého vyplnění koncového kráteru a řízením náběhu proudu při začátku svařování, případně funkcí pro bezdotykové zapalování oblouku HF. Zdroje mohou pracovat s neměnnou, předem nastavenou velikostí svařovacího proudu nebo pracují s tzv. pulsním proudem – periodické střídání jeho vyšší a nižší hodnoty.
Moderní AC zdroje umožní nastavit frekvenci střídání polarity i poměr fází čištění / svařování. Měly by být vždy vybaveny funkcí bezdotykového HF startu.
Pro ruční svařování musí zdroje pracovat se strmou voltampérovou charakteristikou - velikost svařovací proudu se mění minimálně bez ohledu na měnící se vzdálenost hubice hořáku od povrchu svařovaného materiálu tzn., že velká změna délky oblouku = napětí minimálně ovlivní velikost proudu.
Jako ochranná atmosféra inertních plynů je nejčastěji použito helium nebo argon, případně jejich směsi. Vysoká čistota používaných plynů je vyžadována nejenom kvůli omezení opotřebení a zátěže wolframové elektrody, ale také, aby se omezil přístup nežádoucích prvků ke svarové lázni, které mohou způsobit ve svarech vady.
Vadami ve svarech bývají většinou póry a bubliny, které svědčí o nevhodném technologickém postupu, nedostatečné ochraně svarové lázně inertními plyny nebo o použití znečištěných přídavných materiálů nebo svarových ploch.
Této metody se široce používá ke zhotovení vysoce kvalitních spojů v nukleárním, leteckém, chemickém a potravinářském průmyslu.
Kovářské svařování -dvě části se zahřejí na svářecí teplotu 1450°C, kdy je ocel bílá -přiloží se na sebe a údery se ksobě silně přitlačí
-dobře se svařují oceli snižším obsahem uhlíku (do 0,3 %)
-oceli s0,45 % uhlíku se nedají svařovat
-mangan a křemík snižují svařitelnost při svařování kovářským způsobem
-oba díly musí být stejnoměrně zahřáté na svářecí teplotu 1450°C -při nižší teplotě jednoho zkusů materiály ksobě nepřilnou -při vyšší teplotě se ocel spálí -problémy při svařování a ohřevu materiálu silnějších aslabších materiálů -když zvýhně vylétávají jiskry typického tvaru (prskavka), materiál se natavuje -oceli většího průřezu ohříváme pomaleji vcelém průřezu ave výhni občas otočíme kolem své osy, aby se materiál celý prohřál
-topeniště musí být bez škváry a nečistot (vliv na kvalitu sváru) -dosedací plochy se musí co nejméně stýkat se vzduchem, aby nevznikaly okuje -struska se vytvoří pomocí křemičitého písku, svařovacího prášku a boraxu -tyto látky sypeme na svařované konce -po dosažení svářecí teploty materiál rychle vyjmeme, oklepneme strusku a přiložíme ksobě -prokoveme, dokud je materiál tvárný
-průřez se prokováním ztenčí, proto je nutné materiál před svařováním napěchovat -není-li svar dokonalý, spoj znovu ohřejeme a prokoveme -při ohřevu struktura materiálu zhrubne, proto výrobek prokováváme, aby se zjemnila
Tepání
Tepání je tvarování plechu kovotepeckými kladívky s různě tvarovanými úderovými plochami. Technika se používá především pro tvarování nádob a rozměrnější plastické výzdoby (např. na církevních předmětech). Práce se provádí na dřevěném špalku, cizelérském tmelu, koženém vaku s pískem či profilované kovadlině. Pro zlatníka má tepání jednu významnou výhodou – z drahocenného materiálu může vytvořit vizuálně objemné dílo při velmi malé síle plechu. Tepání se často doplňuje jemnějším zpracováním – cizelováním. Pojmy tepání a cizelování se v odborné terminologii často nevhodně zaměňují.
Busta sv. Václava (Svatovítská klenotnice)
Krásný příklad kombinace tepání a cizelování. Základní modelace byla vytepána kladivy ze stříbrného plechu 0,8 mm silného. Hlava, trup, vlasy a čepice byly zhotoveny odděleně a spojeny závlačkami a šrouby. Samotná tvář byla nepochybně tepána podle návrhu, velmi pravděpodobně pomocí dřevěných kadlubů (forem s negativní modelací). Poté byla prokreslena cizelérsky – získala výraz a portrétní rysy.
Cizelování
Cizelování je tvarování, dekorování plechu pomocí čakanů, železných tyček s různě tvarovanými razicími plochami na konci. Čakan drží zlatník v ruce razance úderu dociluje kladívky. Cizelováním se zhotovuje žlábkování, rýhy, vypukliny, důlky, matování ploch; někdy je čakan zhotoven jako malá raznice s drobným dekorem. Z tenkého materiálu vznikají působivé jemné reliéfy a dekorované plochy. Velikou výhodou techniky je možnost střídavě pracovat z obou stran plechu. Plech se obvykle podkládá cizelérskou smůlou, ke které se přilepí zahřátím. Vzácný materiál je úsporně využit – plechy jsou velmi tenké (zpravidla 0,6 mm, výjimkou nejsou skvosty s jen poloviční sílou stěny). Cizelérská technika se též používá při finální úpravě hrubších odlitků (zahlazení, dokreslení modelace).
Plošné rytí
Další technikou zdobení povrchu drahého kovu je plošné rytí. Jemné lineární odebrání materiálu lze přirovnat ke grafice – rydly lze vytvořit nejen plošný ornament, ale celé složité kompozice s různými motivy. Technika se uplatňovala například na liturgických předmětech k vytvoření magických symbolů a božstev. Od gotiky se ryté výjevy vytvořené na rovné ploše kovu začaly využívat k tisku na papír – prohlubně stačilo zatřít černí a lisem přitlačit k papíru. Kalené železné rýtko s dřevěnou násadou, vedené rukou ve správném úhlu, může vytvořit „síť“ drobných vrypů neuvěřitelné jemnosti. Žádnou jinou klasickou grafickou technikou nelze pracovat tak přesně a podrobně – řečeno dnešními slovy, s takovým „rozlišením“. Technicky a kompozičně jsou vrcholnými díly techniky plošného rytí renesanční mědirytiny.
Odlévání
Po období primitivního zpracovávání zlata tepáním byla vynalezena technologie odlévání. Staré národy se naučily tavit kovy v keramických tyglících. Zlato, měď a stříbro, které se v přírodě vyskytují v ryzí (nesloučené) formě, se uplatnily jako první díky snadné zpracovatelnosti bez nutnosti rafinace; teprve později bylo objeveno tajemství výroby bronzů, tavených složitými postupy z rud mědi a zinku. Odlévání ozdobných předmětů z kovů do formiček a především technikou ztraceného vosku bylo známo mnoha kulturám celého světa.
Docílit žáru potřebného k roztavení zlata nebylo obtížné ani v jednoduché výhni. K její stavbě stačilo pár vhodných kamenů na vybudování komůrky a komínového odtahu, vnitřní stěny se vymazaly hlínou. Odlévalo se do formiček ze směsi popele, mastných sazí, jemného jílu a písku, křídy či jiných materiálů, do níž se obtiskl model či reprodukovaný objekt. Poněkud náročnější je odlévání technikou ztraceného vosku – odměnou za pracnost je ale možnost odlít prakticky jakýkoliv návrh zhotovený z vosku, včetně složitých propletenců. Voskový model se obklopí směsí jemné hlíny a křídy; pro zvýšení poréznosti se do druhé vrstvy obalu přidávaly zvířecí chlupy. Po vysušení se forma zahřeje a vosk vyteče ven vtokovým kanálkem. Do vniklé dutiny se nalije roztavený kov a po jeho utuhnutí a vychladnutí se forma rozloží nebo rozbije. Odlitek se většinou dále upravuje a zdobí.
Nanesení a tavba skloviny na povrchu drahého kovu skýtá krásnou možnost, jak lze barevně vykrýt části plochy šperku. Využití emailu na kovech bylo zřejmě objeveno brzy po vynálezu glazury pro zušlechtění keramického střepu. Obě technologie mají společný základ – sklovina probarvená obvykle kysličníky kovů se po utavení rozdrtí na prášek, který se nanese na povrch výrobku. Prášek se v žáru výhně roztaví a sline s podkladem. Emailová sklovina má obvykle nižší tavnou teplotu (750–850 °C) než keramická glazura (1 000–1 200 °C). Slinutí skloviny ve šperkařství musí respektovat tavnou teplotu použité slitiny drahého kovu.
Kdo by neobdivoval jemné krajkoví filigránových šperků? Dráty stáčené do nejrůznějších spirál a rozvilin, pájené do celků, doplněné kuličkou či lístečkem tvoří lehounkou, křehce působící, avšak pevnou konstrukci. Takový fígl se neztratil v žádné zlatnické epoše. Jak se dociluje příznačného jemného zrnění filigránového drátku? Drátek čtverhranného profilu se hustě stočí a následně rozklepe do pásku – na hraně pásku zůstane zrnění. Tvorba složitých ornamentů vyžaduje nejen trpělivost a šikovnost, ale i velkou zkušenost s řazením jednotlivých úkonů. Ke spojení jemné síťoviny se pájka nanáší sypáním jemných pilin.
Granulace
Granulace je půvabná a zdánlivě jednoduchá technika spočívající v nanesení jemných zlatých či stříbrných kuliček na povrch šperku. Má ale hned několik háčků. Jak kuličky vyrobit doopravdy kulaté a stejně velké? Jak je nanést v přesných ornamentech na povrch a připájet je? Techniku granulace, známou již z velkomoravských šperků a během času zapomenutou, rekonstruoval až roku 1932 německý zlatník Wilm. Tajemství spočívá v uchycení kuliček k celku bez použití pájky. Zde je recept: nasekaný materiál, třeba kousky zlatého drátu, se smíchá v tyglíku s rozemletým dřevěným uhlím; v žáru se pak jednotlivé kousky staví do dokonalých kuliček, které se pak přeséváním třídí na skupiny shodných rozměrů. Na povrch zdobeného předmětu se kuličky nanesou pomocí roztoku lepivé pryskyřice v přesně promyšlených obrazcích – víceřadých páscích, trojúhelnících, kosočtvercích srovnaných nasypáním do formiček. A jak se kuličky připájejí k povrchu? Klasické pájení nelze použít – jemné kuličky by se v pájce utopily. Místo toho se využívá poznatku, že kuličky utavené v uhlí mají na povrchu snáze tavitelnou vrstvičku a v žáru se na povrch šperku uchytí i bez pomoci pájky. Šperky zdobené granulací, udivující jemností a přesností rozmístění dekoru, známe zejména z období Velké Moravy.
Montáž
Pojem montáž je poněkud volný – v klasických popisech zlatnických postupů jej obvykle nenalezneme. Přesto jde o nezastupitelnou součást zlatnictví. Tepání i odlévání mají své konstrukční a tvarové limity, nemluvě o hmotnosti výrobku. Proto jsou složité a jemné tvary konstruovány z plechů a z různě kovaných, válcovaných či protahovaných profilů. „Stavební prvky“ vyřezané z plechů a vytvořené z pásků, čtyřhranů, trubiček a drátků se postupně spojují pájením. Montáží lze vytvořit prakticky jakoukoliv konstrukci, výsledek záleží na záměru a zkušenosti, důvtipu a zručnosti zlatníka. Důležitou roli hraje nářadí – ve vybavení zavedené zlatnické dílny najdeme různě tvarované kleštičky, průvlaky na tažení drátů a profilů, kovadlinky s různými rýhami a jamkami, různá kladívka, malé valcny pro válcování plechů a profilů, sadu všelijak tvarovaných pilníků, lupenkovou pilku. Může to být až dva tisíce i více položek; ve srovnání s ostatními řemesly je v tomto pohledu zlatnictví nepochybně rekordmanem.
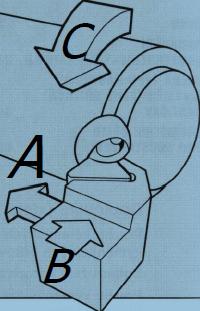
soustružení:
A - podélný posuv
B - příčný posuv
C - Směr otáčení obrobku
Druhy pohybů pří soustružení
při soustružení se otáčí obvykle obrobek, řezný nástroj koná pohyb přímočarý
nástroj koná pracovní pohyb ( podélný, příčný posuv )
dalším důležitým pohybem nástroje je přísuv ( hloubka řezu )
Soustružnické nože
musí mít dobré řezné vlastnosti, musí být tvrdší než obr. materiál, a také co nejodolnější proti opotřebení
jejich tvar a rozměry jsou normalizovány
vyrábějí se z různých materiálů.
Popis soustružnického nože
1 tělo nože
2 základna
3 hlavní ostří
4 hl. hřbet nože
5 špička nože
6 vedl. hřbet nože
7 vedlejší ostří
8 čelo nože
Druhy soustružnických úhlů
úhel hřbetu α – ovlivňuje velikost tření mezi plochou hl. hřbetu a řeznou plochou.
úhel břitu β – má vliv na odpor, který klade materiál obrobku noži při soustružení.
Úhel čela γ – ovlivňuje velikost řezného odporu
Úhel řezu δ – je součet úhlu hřbetu a břitu
Úhel špičky ε – ovlivňuje jakost obrobeného povrchu a stabilitu břitu
Materiály destiček s. nožů
s řeznou destičkou z SK- mají velkou tvrdost a odolnost proti otěru.Jsou vhodné k obrábění běžných materiálů. Nedostatkem je křehkost a nízká pevnost v ohybu. Tento materiál je nejpoužívanější.
S keramickými ř. destičkami- mají nízkou pevnost
Kubický nitrid boru – používá se na tepelně upravované - kalené materiály
Materiály destiček s. nožů
s řeznou destičkou z SK- mají velkou tvrdost a odolnost proti otěru.Jsou vhodné k obrábění běžných materiálů. Nedostatkem je křehkost a nízká pevnost v ohybu. Tento materiál je nejpoužívanější.
S keramickými ř. destičkami- mají nízkou pevnost
Kubický nitrid boru – používá se na tepelně upravované - kalené materiály
Soustružnické nože tvarované
Soustružnické nože tvarové
tvarové nože- tyto nože používáme v sériové výrobě.Přesnost a kvalita jimi obrobených ploch je vysoká.Výroba je velmi náročná a složitá.Rozdělují se na radiální a tangenciální.
Přesnost a jakost při soustružení: IT Ra
- práce na čisto IT 7 – 9 Ra 1, 6 – 6, 3
- jemné soustružen IT 6 – 8 Ra 0, 8 – 1, 6
je to jemné soustružení při velké řezné rychlosti, při tom je potřeba zajistit dostatečné chlazení aby nedocházelo ke změnám velikosti vlivem působení teploty
Univerzální hrotový soustruh
Revolverový soustruh
v současné době méně používaný, nahrazen CNC stroji
Lícní soustruh
Svislé soustruhy - karusely
Dvoustojanový svislý soustruh
Rovinné plochy frézujeme za účelem dosažení předepsané rozměrové a tvarové přesnosti a jakosti povrchu frézami válcovými nebo čelními válcovými frézami - větší plochy frézujeme frézovacími hlavami.
Při frézování rovinných ploch dodržujeme tyto zásady:
- zvolit vhodný typ stroje, nástroje a upínače
- pokud je možné použít čelního frézování, které je výkonnější a kvalita obrobené plochy je lepší než při frézování válcovými frézami.
- pečlivě očistit upínací plochy stolu, obrobku, fréz a frézovacích trnů.
- používat klíčů správných rozměrů.
- obrobené plochy chránit při upínání měkkými podložkami,
- při výškovém nastavení zajistit konzolu, při frézování se záběrem podélného stolu je třeba zajistit příčné saně, při záběrem příčných saní zajistit podélný stůl,
- obrobkem je třeba pod frézou pohybovat opatrně, aby se prudkým nárazem fréza nepoškodila,
- otupenou frézu okamžitě vyměnit,
- při měření je třeba očistit obrobek a zbavit jej otřepů.
Frézování rovinných ploch válcovými frézami
Osa frézy je rovnoběžná s obráběnou plochou – obr. 2. Šířka frézy musí být větší než šířka frézované plochy. Používáme dva způsoby frézování: sousledné a nesousledné.
Nesousledný způsob - fréza se otáčí proti smyslu pohybu obrobku. Tříska tvaru ohnutého trojúhelníku je tvořena od minimální tloušťky po maximální tloušťku při vyjetí zubu ze záběru. Výhody: práce frézy je klidná bez rázů, uplatňuje se při frézování odlitků a výkovků s tvrdou povrchovou kůrou. Nevýhody: břit zpočátku neřeže, klouže po materiálu obrobku, než dosáhne minimální tloušťky třísky 0,01 až 0,03 mm,čímž se zvyšuje řezný odpor a teplota řezání a tím se zvyšuje opotřebení břitu nástroje a zhoršuje se kvalita obrobené plochy. Dále je obrobek řeznou silou vytahován z upínače, proto je nutné použít vetší upínací síly, což se nehodí pro tenkostěnné obrobky s malou tuhostí.
Sousledný způsob – fréza se otáčí ve stejném smyslu s pohybem obrobku. Tříska se tvoří od maximální tloušťky po minimální tloušťku při výjezdu zubu frézy ze záběru.
Výhody: fréza po materiálu neklouže, tím vzniká méně tepla, fréza se nezahřívá a, proto je možné volit vyšší řeznou rychlost větší posuv. Obrobek je řeznou silou přitlačován do opěrných ploch upínače, což umožňuje upínat tenkostěnné obrobky při velkých hloubkách řezu. Nevýhody: frézování je nárazové vyžadující vymezení vůlí ve vodících plochách a posuvových mechanismech, aby vznikající chvění nezhoršilo kvalitu povrchu obráběné plochy a popřípadě zničení nástroje.
Frézování rovinných ploch válcovými čelními frézami
Při čelním frézování je osa rotace frézy kolmá k obráběné ploše. Jednotlivé zuby odřezávají třísky téměř stejného průřezu, takže tloušťka třísky se mění jen málo. Zatížení nástroje i stroje je během řezání prakticky stálé, chod stroje je plynulý a rovnoměrný, chvění je velmi malé. Zuby materiál odřezávají na obvodě frézy,na čele frézy obrobenou plochu jen hladí. Kvalita obrobené plochy je lepší než při válcovém frézování. Průměr frézy se podle možností volí asi 2x větší než šířka frézované plochy – obr. 3.
Výhody čelního frézování:
- produktivnější než obvodové frézování-umožňuje odfrézovat větší množství třísek,
- používají se frézy větších průměrů zejména frézovací hlavy-větší tuhost nástroje,
- upnutí frézy je tužší-upínají se za krátký trn nebo za stopku,
- frézování je klidnější, neboť v záběru je několik zubů současně a tloušťka třísky se mění jen nepatrně.
Vady při frézování rovinných ploch
a) rozměry součásti neodpovídají rozměrům na výkrese- příčina: nesprávné upnutí obrobku, nepozorné měření, nebo špatně nastavená hloubka řezu
b) horší kvalita povrchu než je předepsána – příčina:házení frézy, tupá fréza, malý nebo velký posuv na zub sz (mm/zub)
c) povrch obrobku se stopami po nástroji způsobuje protočení frézy na jednom místě, přemístění obrobku do výchozí polohy pod otáčející se frézou-opačný pohyb než při frézování.
d) vlnitý a nerovný povrch obrobené plochy způsobuje házení frézy nebo frézovacího trnu
e) poškozený otlačený povrch součásti bývá způsoben použitím tvrdého kladiva při doklepávání obrobku nebo upnutí bez ochranných vložek z plechu.